In the pharmaceutical field, many companies use filter cloth for filtration in agitator filter dryers. However, as the environment changes and viruses mutate faster and faster, people’s demand for pharmaceuticals is getting higher and higher, which requires manufacturers to improve production efficiency.
1. The Disadvantages of Filter Cloth Used For Pharmaceutical Material Filter
1) Poor Wear Resistance, Needs to Replace Filter Cloth Frequently
2) Cause Heat Loss and Electricity Waste
2. Sintered Wire Mesh Plate Advantages
1) The Surface Layer of Sintered Wire Mesh Plate Is More Wear Resistance And Stronger
2) Heat Lost Reduced And Saves Electricity
3) The aperture of the Sintered Wire Mesh Plate is Uniform
4) Sintered Wire Mesh Plate Resist High Pressure Drop
5) Cleaning Of Sintered Wire Mesh Plate
Are you still using filter cloth to filter pharmaceutical materials?
Can your production efficiency meet customer needs?
Are you still worried about frequent shutdowns to change filter clothes?
The filter cloth is used popularly because of its low price. Main material is PP, Nylon and so on.
1. The Disadvantages of Filter Cloth Used For Pharmaceutical Material Filter
1) Poor Wear Resistance, Needs to Replace Filter Cloth Frequently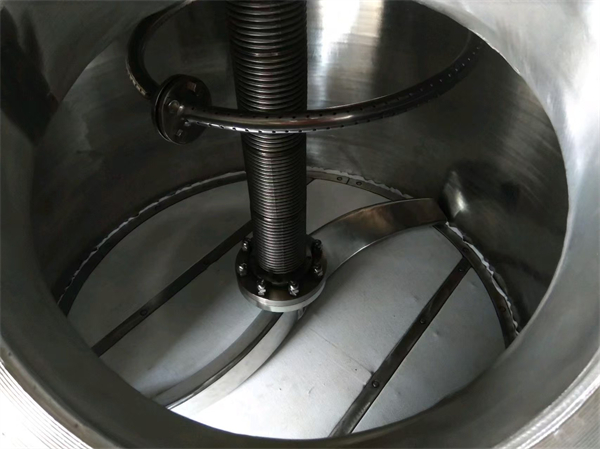
During the agitating process, friction will occur between the filter cloth and the material. Since the filter cloth is very thin and has poor wear resistance, it is easy to break it. The company has to stop production to change the clothes. Generally, companies change it every 2-3 months, which affects production efficiency.
2) Cause Heat Loss and Electricity Waste
In addition, the equipment needs to heat and dry the material. During shutdown, heat will be lost. Manufacturer needs to reheat, resulting in a waste of electricity.
The sintered wire mesh plate could avoid the above problems. It’s several layers of metal wire cloth laminated together.
2. Sintered Wire Mesh Plate Advantages
1) The Surface Layer of Sintered Wire Mesh Plate Is More Wear Resistance And Stronger
The sintered wire mesh plate is several layers laminated together. The surface layer next to the scraper is coarse mesh with thick wire diameter, which is more wear-resistant, and much stronger than filter cloth. So it can be used for a much longer time. The shutdown time is shortened greatly and improves efficiency a lot.
2) Heat Lost Reduced And Saves Electricity
Frequent shutdowns is avoided, reducing heat loss. Electricity is saved.
3) The aperture of the Sintered Wire Mesh Plate is Uniform
The sintered wire mesh plate maintains the original mesh diameter and uniform aperture during the firing process, and the size of the particles after filtration is uniform.
4) Sintered Wire Mesh Plate Resist High Pressure Drop
The sintered wire mesh plate could resist the same high-pressure drop as the perforated plate.
5) Cleaning Of Sintered Wire Mesh Plate
Users only need to remove the sintered wire mesh plate and clean it with a pulse when the filtration efficiency is low.
We have advanced sintering equipment and a first-class technical team to provide tailored solutions and services. If you have any needs, pls don’t hesitate to get in touch with us at info@alloyfilter.com